Drill pipes are a crucial component of the drill string, playing a vital role in the drilling process. Their primary functions include transferring drilling mud to the drill bit, working with the drill bit to lift, lower, or rotate the bottom hole assembly, and withstanding significant internal and external pressure, torque, bending, and vibration. Thus, the manufacturing process of drill pipes must be meticulously controlled to ensure their reliability and durability in harsh drilling environments. Drill pipe is an indispensable key component in drilling operations. Its main functions include effectively transferring drilling mud to the drill bit, connecting the drill collar at the bottom, and lifting, lowering or rotating the bottom hole device together with the drill bit. The drill pipe not only bears huge internal and external pressure and torque, but also has to withstand bending and vibration during the drilling process. The standard of drill pipe is API 5CT. In order to ensure that the drill pipe can operate stably in harsh drilling environments, its manufacturing process must be finely optimized.
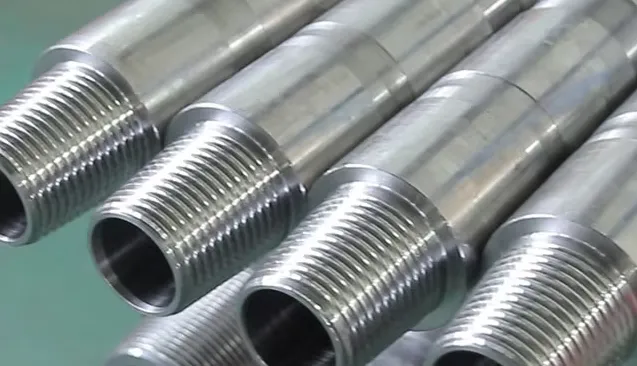
What are the manufacturing processes of drill pipe?
Below is a detailed description of the manufacturing process for oil drill pipes:
1. Raw Material Preparation
Material Selection
The pipe body of oil drill pipes is typically made from low-carbon alloy steel. This type of steel has excellent strength and toughness, making it suitable for high-pressure and high-temperature conditions. The choice of raw material is crucial as it directly affects the performance and lifespan of the drill pipes.
Material Inspection
Before production begins, the selected steel must undergo rigorous chemical composition analysis and physical performance testing to ensure it meets relevant standards and requirements.
2. Pipe Body Processing
Continuous Casting and Rolling
Steel billets are initially shaped into pipe body forms through continuous casting and rolling processes. This technique involves cooling the molten steel through casting molds, followed by rolling to form the preliminary shape of the pipe. The focus here is on ensuring that the pipe body’s shape and dimensions meet the specifications.
Heating and Piercing
The round steel billets are heated to the appropriate temperature in a large rotary furnace before being sent to an elongator and automatic piercing mill for piercing. The purpose of heating is to increase the steel’s plasticity, facilitating subsequent processing and shaping.
Internal and External Diameter Sizing
The pierced pipe body then undergoes internal and external diameter sizing to ensure dimensional accuracy. This process is performed using precision machining equipment to achieve a smooth and uniform surface on both the inside and outside of the pipe.
Straightening
After diameter sizing, the pipe body must be straightened to maintain its linearity. This process removes any curvature and deformation from the pipe, ensuring its stability and accuracy for further processing.
3. Pipe End Thickening
Heating and Uniform Heating
The ends of the pipe require heating and uniform heating treatment to enhance their plasticity, making them easier to shape during the swaging process. This involves heating the pipe ends to a specific temperature and holding them there for a period to ensure uniform material properties.
Swaging
The pipe ends are swaged using hydraulic or pneumatic methods to increase their thickness. This process enhances the strength and durability of the pipe ends. During swaging, the outer surface is shaped using molds, while the inner surface forms naturally through temperature gradients.
Heat Treatment and Inspection
The entire pipe body undergoes heat treatment, including annealing, quenching, and tempering, to improve its overall performance. Each stage of the heat treatment process is carefully monitored to ensure product quality. Non-destructive testing is also conducted to detect any internal defects.
4. Tool Joint Processing
Hot Forging
Tool joints are manufactured from medium-carbon alloy steel and are hot forged into shape through multiple stamping processes. This step aims to form the joint components into the desired shape for further processing and heat treatment.
Machining
The joints are then machined for internal holes, external diameters, and end faces to achieve precise dimensions and shapes. This machining process ensures the accuracy and surface quality of the joints.
Heat Treatment
The joints undergo quenching and tempering heat treatments to obtain excellent mechanical properties. Modern drill pipe manufacturers use fully automated continuous controlled atmosphere heating technology to ensure consistent quality and efficiency in heat treatment.
Threading and Protection
High-precision threading is performed on the joints, and the surface is treated with copper plating or phosphating to prevent seizing during use. The precision of the threading affects the connection performance of the drill pipes, and protective treatments extend the joints' service life.
5. Friction Welding and Final Processing
End Processing
The ends of the pipe body and joints are processed to ensure the flatness and accuracy of the joining surfaces. This precise end processing is crucial for the quality of the welding and the performance of the finished product.
Friction Welding
The processed pipe body and joints are then joined using friction welding, forming a complete drill pipe. Friction welding is advantageous due to its high weld quality and fast production efficiency, effectively enhancing the strength and stability of the weld area.
Weld Treatment
The welds are subjected to annealing, finishing, quenching, and tempering to improve their strength and toughness. These treatments ensure that the welds have excellent mechanical properties and can perform reliably under high pressure and temperature conditions.
Inspection and Marking
The finished drill pipes undergo thorough inspection to detect any internal defects. Additionally, the pipes are marked with product information and production batches for traceability and management.
Manufacturing Process of Oil Drill Pipe
Summary
The manufacturing process of oil
drill pipes encompasses several key stages, including raw material preparation, pipe body processing, pipe end thickening, tool joint processing, and friction welding with final processing. Each stage requires strict quality control and technical parameters to ensure that the product meets drilling requirements. Through high-standard manufacturing processes and meticulous quality control, oil drill pipes can provide reliable support in complex drilling environments, ensuring the smooth progression of drilling operations.