Piling Pipe
The popularity and application of pipe piles has grown by leaps and bounds since the late 1980s. An extensive series of tests proved pipe piles' effectiveness in bearing loads, their use in civil construction exploded and pipe pile suppliers began to grow their business more. If your industry includes large loads, you should be familiar with pipe piling. In recent years, deep-water wharf projects have been constructed on a large scale. As the main bearing capacity of deep-water wharf pile foundations, spiral welded large-diameter steel pipe piles are commonly used. In addition, piling pipes are required for bridge construction, road construction, high-rise buildings, etc.
It is a pipe made of welded,
spiral welded . Pipe piles are used in industries involving heavy loads or deep foundation structures. Piles are driven into the ground and can be closed or open. Piles ensure good resistance to frictional loads due to their large surface area for interaction with the surrounding soil. Pipe piles are made of steel and therefore can withstand extremely heavy loads. In addition, steel pipe piles are also commonly used in bridge, building, marine, railway, and highway construction.
General symbols
D: Nominal outer diameter of steel pipe, mm
T: nominal wall thickness of steel pipe, mm;
M: Steel pipeline mass, kg/m
Manufacturing method
Spiral steel pipe is a spiral seam steel pipe welded by automatic double-wire double-sided submerged arc welding process using strip steel coil plate as raw material, regular temperature extrusion molding.
(1) Raw materials include steel strip coil, welding wire and flux. They must undergo strict physical and chemical inspections before being put into use.
(2) The head and tail of the steel strip are butt-jointed using single-wire or double-wire submerged arc welding. After being rolled into a steel pipe, automatic submerged arc welding is used for repair welding.
(3) Before forming, the strip steel is leveled, trimmed, planed, surface cleaned, transported and pre-bent. (4) Electric contact pressure gauges are used to control the pressure of the cylinders on both sides of the conveyor to ensure smooth transportation of the strip.
(5) Adopt external control or internal control roller forming.
(6) A weld gap control device is used to ensure that the weld gap meets the welding requirements. The pipe diameter, offset amount and weld gap are all strictly controlled.
(7) Both internal and external welding use American Lincoln welding machines for single-wire or double-wire submerged arc welding to obtain stable welding specifications.
(8) All completed welds have been inspected by an online continuous ultrasonic automatic flaw detector, ensuring 100% non-destructive testing coverage of spiral welds. If there is a defect, it will automatically alarm and spray mark, so that production workers can adjust the process parameters at any time to eliminate defects in time.
(9) Use an air plasma cutting machine to cut the steel pipe into individual pieces.
(10) After cutting into individual steel pipes, the first three steel pipes in each batch must undergo a strict first inspection system to check the mechanical properties, chemical composition, fusion status of the welds, the surface quality of the steel pipes, and non-destructive testing to ensure the pipe making process Only after passing the test can it be officially put into production.
(11) The areas with continuous sonic flaw detection marks on the welds will undergo manual ultrasonic and X-ray re-examination. If there are indeed defects, they will be repaired and then undergo non-destructive inspection again until it is confirmed that the defects have been eliminated.
(12) The pipes where the strip butt welds and the T-shaped joints intersecting the spiral welds are located must be inspected by X-ray television or film.
(13) Each steel pipe has undergone a hydrostatic pressure test, and the pressure is radially sealed. The test pressure and time are strictly controlled by the steel pipe water pressure microcomputer detection device. Test parameters are automatically printed and recorded.
(14) The pipe end is machined to accurately control the end face verticality, bevel angle and blunt edge.
Pipe pile installation
In order to install a pipe pile, a pile driver is required. Pile drivers are machines that are capable of driving the piles deep into the ground using hydraulic systems that can exert high levels of force. When steel piles are driven directly into the soil, without the need for drilling a hole, the soil itself provides the necessary support for stabilizing the pipe. As the pipe is driven into the ground, the soil is displaced, creating increased friction and pressure from all sides, which helps to firmly hold the pipe in place.
Methods to place the piling pipe
Depending upon the load of the building at different locations, engineers and installers shall decide the placement of the pipe. When there is a very heavy load, typically in the case of industrial equipment, the pile pipe must be placed directly under it, so that it offers enough support.
If the load distribution of the building is even, there might be a concrete pile cap that is used for supporting the building, which allows the piling pipe for equal placement and serves as a single assembly connector for the entire foundation.
Choosing the right steel pile pipe for piling
The pipe piling must be chosen carefully depending on the forces of the building, the prevailing conditions of the soil and building codes of that area. The placement of piles is determined by a geotechnical engineer. The structural engineer then decides on the piling material, and size of the pipe piling according to the depth which they must reach. In cases where a single piling pipe does not reach the required depth, piles are joined using splicing sleeves or butt welds to make them longer.
How does steel pile pipe work?
Steel piles are utilized in situations where the soil beneath a building is loosely packed, and there are concerns about the long-term stability of the structure. By using a pipe pile, the weight is evenly distributed and extends deeper into the Earth, where the soil is more compact. This proves to be highly advantageous in the construction of super-large buildings, where the soil alone cannot provide the necessary support.
On the other hand, in situations where the land area is small and does not give enough room for spread footers or foundations, the forcing buildings will be used so that there is a better level of stability on the ground.
Common forms of pipe piling
The most commonly used forms of pile pipes are typically large in diameter, ranging from 16 inches to 60 inches. These heavy-duty steel pipes can be manufactured using longitudinal welded (LSAW), or spiral welded (SSAW) techniques. Depending on the soil environments, the pipes may be coated with zinc (galvanized), FBE, or 3LPE coatings. This helps to provide moisture resistance and corrosion resistance, enhancing their durability.
Pipe piling size
Normally, piling pipe OD ranges from 250 mm (10 inch) to 1500 mm (60 inch), thickness from 8 mm to 25 mm.
Referred standard specification of pipe pile
The most widely used standard for pipe pile is
ASTM A252. Grades in three levels, Gr 1, Gr 2, and Gr 3.Chemical Composition of ASTM A252: The steel only defines no more than 0.050 % phosphorous.This specification is generally for wall steel pipes that are cylindrical in shape. The steel cylinder acts like a load-carrying member for the cast-in-place piles of concrete.
Types of Manufacturing for pipe piling
Pipe piling is generally manufactured using resistance welding, fusion welding, flash welding with seams being longitudinal, helical. It also specifies the tensile requirements, minimum values and the common size and weight based on the values.
Advantages of steel pipe pile
One of the major advantages of steel pipe piles is their ability to provide robust support for underground foundations. This is particularly important when a structure needs to bear a heavy load, as it necessitates a deep and strong foundation. Therefore, having the appropriate structural support, such as steel pipe piles, is crucial for ensuring the stability and strength of deep foundations.
Although there are various options for structural support available, steel pile pipes are highly recommended due to their versatility and customization capabilities. Steel pile pipes can be tailored to meet specific requirements, making them an ideal choice. Additionally, the cost associated with using steel pile pipes is relatively minimal compared to other alternatives.
Less cost
When purchasing pipe piles, there is no need for additional expenses on structural support as the construction and erection process is relatively simple and less complex. Furthermore, pipe piles can be tested before they are used, ensuring their quality and reliability. Moreover, pipe piles are easy to add after the initial construction phase, making them a convenient choice. In terms of maintenance and replacement costs, pipe piles are considered to be the most cost-effective option, making them an efficient choice for structural support.
Free of cracking
Steel pipe piles are resistant to cracking during the driving process and can effectively support heavy loads. They are also easy to handle and install, making them user-friendly. When properly installed, steel pipe piles have minimal overall costs and provide a high level of safety.
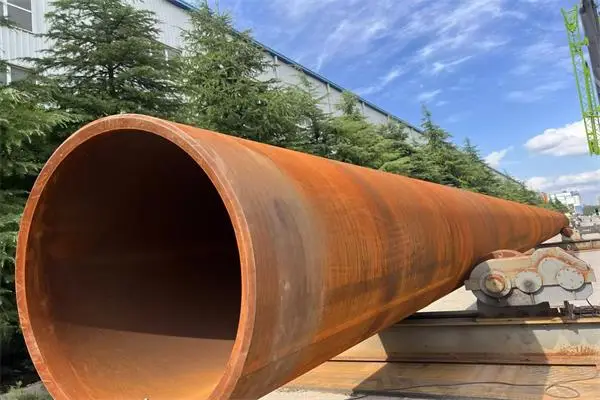
Baowi-steel Supplies Pipe Pile
Reach out to us and we will offer you the best solutions, products, implementations, design and workforce to ensure that your deep foundation is strong and safe.
When conditions permit, pipe piles have become one of the most effective heavy-duty support alternatives in the industry. Our pipe pile supplier customers get support systems that are thoroughly optimized for cost and safety under the proper expert supervision. Our international pipe suppliers use designers, the best materials and piling machines, and work directly with customers every step of the way to ensure the best results for their pipe piling.