Carbon steel is a type of steel with a carbon content between 0.02% and 2%, and very few other elements. It is also the metal material with the highest output.
Carbon steel is divided into high carbon steel, medium carbon steel and low carbon steel. The higher the carbon content, the higher the hardness, strength and wear resistance of the steel after heating treatment, and the more brittle it is. The lower the carbon content, the softer and more ductile it is.
It is usually used on metal parts that require strength, hardness and wear resistance, such as cutting tools, steel cables, piano wires, springs and knives. After processing, the parts usually need to be processed and tempered.
Characteristics of low carbon steel, medium carbon steel and high carbon steel
Low carbon steel (mild steel) is carbon steel with a carbon content of less than 0.25%. It is also called mild steel because of its low strength, low hardness and softness. It includes most ordinary carbon structural steels and some high-quality carbon structural steels. Most of them are used for engineering structural parts without heat treatment, and some are used for mechanical parts requiring wear resistance after carbon and other heat treatments.
Medium carbon steel has good hot processing and cutting performance, but poor welding performance. The strength and hardness are higher than those of low carbon steel, while the plasticity and toughness are lower than those of low carbon steel. Cold rolled and cold drawn materials can be used directly without heat treatment, or they can be used after heat treatment. Medium carbon steel has good comprehensive mechanical properties after quenching and tempering. The highest hardness that can be achieved is about HRC55 (HB538), and ob is 600~1100MPa. Therefore, medium carbon steel is most widely used in various uses with medium strength levels. In addition to being used as a building material, it is also widely used in the manufacture of various mechanical parts.
High Carbon Steel is often called tool steel, with a carbon content ranging from 0.60% to 1.70%. It can be quenched and tempered, and has poor welding properties. Hammers, crowbars, etc. are made of steel with a carbon content of 0.75%; cutting tools such as drills, taps, reamers, etc. are made of steel with a carbon content of 0.90% to 1.00%.
History of High Carbon Steel
High carbon steel is more than just an ordinary metal. It has a long history that dates back centuries and has been used in a variety of fields from swords to industrial machinery. Legend has it that the famous samurai swords of ancient Japan were made of high carbon steel, giving them legendary sharpness and strength.
In modern times, high carbon steel remains a popular choice for a wide range of applications due to its durability and versatility. Whether you are in the market for a trustworthy knife or need a reliable material for your manufacturing needs, high carbon steel is a tried and true choice that will not let you down. So let's take a deep dive into the world of high carbon steel and see what makes it so special.
Definition of High Carbon Steel
High carbon steel is a type of steel that has a higher carbon content than other steels. Typically, it has a carbon content of 0.60% to 1.5%. This results in a harder and stronger material that is often used for tools and machine parts that require high durability and strength.
Composition and Classification of High Carbon Steel
High carbon steel typically contains 0.6% to 1.0% carbon, but some special grades may contain more than 1.0%. This high carbon content directly affects the metal's microstructure, resulting in increased hardness and strength, but reduced ductility. In short, higher carbon content promotes the formation of carbides within the steel matrix, making the material harder and more wear-resistant.
Compared to low carbon and medium carbon steels, high carbon steels have excellent tensile strength and hardness, but poor ductility. Low carbon steels (less than 0.3% carbon) are generally more ductile and easier to weld, while medium carbon steels (0.3% to 0.6% carbon) strike a balance between strength and formability.
From an engineering perspective, the unique composition of high carbon steel makes it advantageous for products that must withstand frequent use, repeated impact, or long-term wear, as these factors often require enhanced hardness.
Below is a table of common high carbon steel grades
Element
|
Standard
|
Carbon Content (%)
|
Main Features
|
Typical Applications
|
AISI 1060
|
SAE / AISI
|
~0.55–0.65
|
Can be heat-treated to achieve load-bearing hardness; moderate wear resistance
|
Springs, large blades, forgings
|
AISI 1070
|
SAE / AISI
|
~0.65–0.75
|
High strength and wear resistance; good impact toughness after quenching
|
Springs, tools, heavy-duty parts
|
AISI 1080
|
SAE / AISI
|
~0.75–0.88
|
Heat-treatable for hardness; similar ductility to mild steel
|
Blades, cutting tools, punches, molds
|
AISI 1095
|
SAE / AISI
|
~0.90–1.03
|
High hardness, good toughness, strong edge retention in cutting tools
|
Knives, springs, industrial cutting tools
|
SK5
|
JIS (Japan)
|
~0.80–0.90
|
Similar to AISI 1080–1085; good wear resistance, can be hardened to a high degree
|
Saw blades, chisels, metal cutting tools, hand tools
|
Standard
|
Grade
|
Application
|
ASTM A29/A29M
|
AISI/SAE 1060
|
Springs, gears, axles, heavy-duty machinery components
|
ASTM A29/A29M
|
AISI/SAE 1065
|
Springs, cutting tools, industrial knives and blades
|
ASTM A29/A29M
|
AISI/SAE 1070
|
Springs, automotive suspension components, agricultural machinery parts
|
ASTM A29/A29M
|
AISI/SAE 1080
|
Heavy-duty springs, automotive components, heavy machinery parts
|
ASTM A295
|
AISI/SAE 52100
|
Bearing steel used in the manufacture of ball and roller bearings
|
ASTM A600
|
AISI/SAE M2
|
High-speed tool steel used for cutting tools, drills, and taps
|
ASTM A686
|
AISI/SAE W2
|
Water-hardening tool steel used for cutting tools, dies, punches, and woodworking tools
|
Properties of high-carbon steel
Because standards and grades vary between each other, there is no one value for the properties of high-carbon steel. Below is a broad range of what you can expect.
Property
|
Value
|
Density
|
0.0163 – 0.298 lb/in³
|
Tensile Strength, Yield
|
39900 – 484000 psi
|
Fracture Toughness
|
12.0 – 150 ksi-in½
|
Shear Modulus
|
11300 – 12000 ksi
|
Melting Point
|
2,800-2,900°F
|
Thermal Conductivity
|
1132 – 361 BTU-in/hr-ft²-°F
|
The differences between low, medium and high-carbon steel
The essential difference is in the steels’ carbon content, which gives each different characteristics.
|
Low-carbon steel
|
Medium-carbon steel
|
High-carbon steel
|
Carbon Content
|
0.05% to 0.32%
|
0.30% to 0.60%
|
0.60% to 1.5%
|
Characteristics
|
Ductile
|
Stronger
|
Very strong
|
Malleable
|
Harder
|
Very hard
|
Tough
|
Less ductile
|
Poor ductility
|
Easily joined and welded
|
Less malleability
|
Poor malleability
|
Poor corrosion resistance
|
Good corrosion resistance
|
Better corrosion resistance
|
What are the advantages and disadvantages of high carbon steel?
One of the main advantages of high carbon steel is its excellent hardness and wear resistance, making it ideal for applications such as cutting tools, springs, and high-strength wire. In addition, it has good tensile strength and can withstand high levels of stress and pressure.
However, there are some disadvantages to using high carbon steel. It has poor weldability, making it challenging to work with, and it is more brittle than other types of steel. In addition, high carbon steel is susceptible to rust and corrosion if not properly treated or coated.
Performance of High-Carbon Steel
1.High Hardness – The elevated carbon content in high-carbon steel enhances the bonding between carbon and iron, leading to the formation of abundant carbides. This significantly increases the steel’s hardness and strength.
2.Superior Strength – Through heat treatment methods such as oil or water quenching, high-carbon steel not only achieves greater hardness but also enhances its tensile strength, making it a highly durable material.
3.Moderate Toughness – While high-carbon steel offers better toughness compared to other ultra-hard steels, it is still less ductile than low-carbon steel.
4.Excellent Wear Resistance – Due to its high hardness, high-carbon steel exhibits strong wear resistance, making it ideal for manufacturing hammerheads, blades, needles, and other abrasion-resistant products.
5.Brittle Nature – The high carbon content increases brittleness, requiring careful handling during manufacturing and usage to prevent fractures or sudden breakage.
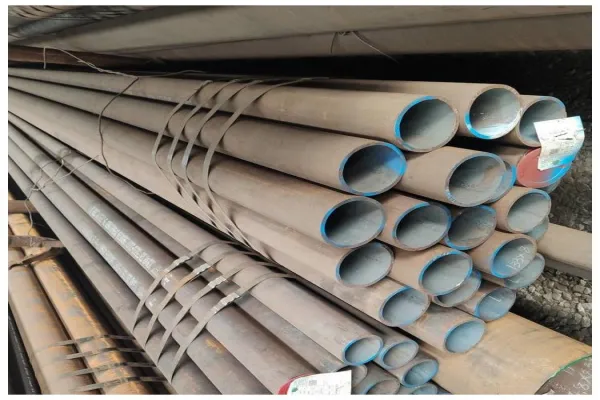
The uses of high-carbon steel
High-carbon-steel uses include anything needing wear resistance and durability, as shown in the table below. High-carbon steel is often used to manufacture springs. A note about plain high-carbon steel, which is often used to mean high-carbon steel. They are different. Plain high-carbon steel consists mostly of carbon and iron, without any significant amounts of alloying elements.
Manufacturing Process of High-Carbon Steel Pipes
The production of high-carbon steel pipes involves multiple stages, including melting, forming, and heat treatment to enhance performance. The typical steps include:
Steelmaking – The raw materials, primarily iron ore and carbon additives, are melted in a blast furnace or electric arc furnace.
Forming – The molten steel is cast into billets or ingots, which are then rolled into pipe shapes using
seamless pipe or
welded pipe manufacturing techniques.
Heat Treatment – Processes such as quenching and tempering enhance the hardness, strength, and toughness of the pipes.
Finishing & Inspection – The pipes undergo machining, surface treatments, and quality control checks to meet industry standards.
Applications of High-Carbon Steel Pipes
Due to their exceptional strength and wear resistance, high-carbon steel pipes are widely used in industries such as:
Oil & Gas Industry – Used in drilling and pipeline systems that require strong, wear-resistant pipes.
Construction & Structural Engineering – Applied in high-strength frameworks, bridges, and load-bearing structures.
Manufacturing & Heavy Machinery – Utilized in machine parts, tool components, and impact-resistant equipment.
Automotive & Transportation – Found in axles, shafts, and high-strength components.
Defense & Military – Used in armor plates, ballistic protection, and high-impact structural components.
Comparison of welding performance between low carbon steel and high carbon steel
The quality of steel welding performance mainly depends on its chemical composition. The most influential element is carbon, that is, the amount of carbon in the metal determines its weldability. Most of the other alloying elements in steel are also not conducive to welding, but their influence is generally much smaller than that of carbon. Generally, low carbon steel has good weldability and generally does not require special process measures. Only when it is low temperature, thick plate or has higher requirements, it is necessary to use basic welding rods for welding and preheat appropriately. When the carbon and sulfur content in low carbon steel are both biased towards the upper limit, in addition to requiring the use of high-quality low hydrogen welding rods, taking preheating and post-heating measures, it is also necessary to reasonably select the groove form and reduce the fusion ratio to prevent the occurrence of hot cracks.
Medium carbon steel has a tendency to cold crack when welding. The higher the carbon content, the greater the tendency of hardening in the heat affected zone, the greater the tendency of cold cracking, and the worse the weldability. As the carbon content of the parent material increases, the carbon content of the weld metal will also increase accordingly. Coupled with the adverse effects of sulfur, hot cracks are easily formed in the weld. Therefore, medium carbon steel welding should use alkaline welding rods with good crack resistance, and take preheating and post-heating measures to reduce the tendency of cracks.
When welding high carbon steel, due to the high carbon content of this steel, it will produce great welding stress during welding, and the hardening and cold cracking tendency of the welding heat affected zone is greater. At the same time, welding is more likely to produce heat. Cracks, high carbon steel is more likely to produce hot cracks than medium carbon steel, so this type of steel has the worst weldability, so it is not used in general welding structures, and is only used for casting repair welding or surfacing. After welding, the weldment should be tempered to eliminate stress, fix the structure, prevent cracks and improve performance.